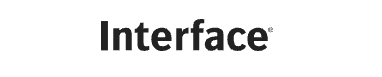
Client – Interface : Carpet Tile Manufacturing
This is the story of how Meteor Software Ltd helped Interface’s inspirational engineers eliminate waste. We often hear about streamlining, lean manufacturing and cost reduction, but this project took waste management in Interface to a whole new level. It ruptured a continuous cycle of waste that was costing millions.
Ask for help with your industry
What Do Interface Do?
Interface make carpet tiles. Using yarn that is bought in from suppliers across the globe, they produce beautiful, eye-catching flooring in their plant in Craigavon, Northern Ireland. They supply into the corporate offices of many very well known global brands, bringing their client’s offices to life.
Innovation never stops
New designs need trial runs
Interface have some products that they keep getting repeat orders for, but they also focus on creation of new patterns and textures to catch the eye of their clients..
Waste Created
As with all new product development, a lot of waste is created. The search for product market fit generates lots of products that just don’t make it to become commercially successful. Each design may have had a few hundred square meters produced as a trial, never to be used again. Even when a design piques a client’s interest and a few thousand square meters are produced, a volume of yarn that is ordered – often with unique colours, is returned to the warehouse. It is not dumped, recycled or put to any other product, in the hope that the prospective client will place an order.
Ongoing Problem
Over time, the volume of unusable yarn in the warehouse builds up, and eventually is written off – costing hundreds of thousands, sometimes millions of pounds. It’s an uncomfortable decision to take, and is often put off from one financial year to the next.
Kicking The Can Down The Road
A big problem for this industry is the chaos created by unusable stock that is returned to the warehouse. At the time when it is returned to the warehouse, there’s no reason to think that the yarn is usable. The cost of the material is the largest factor, but there’s also the cost of providing clean, dry, accessible storage space. Over time, this ticking taxi-meter type of cost becomes significant. Nobody really tracks this well and other operational requirements take precedence. The wasted journeys taken by forklift trucks going backwards and forwards between the warehouse and factory floor, as well as the potential for accidental damage and product degradation over time all exacerbate the problem.
Taking The Bull By The Horns
Interface wanted to eliminate this waste, and their new product development manager had an idea.
Operational Opportunity
Carpet production involves supplying individual cones of yarn to the rear of a loom. With the advanced patterns, each cone will be used up to a greater or lesser extent for a given area of carpet produced. Ryan’s idea was to calculate this length, and supply just enough yarn onto each cone, so that when the run ended there would be zero, or effectively zero yarn left on the cone. This would stop the cycle in its tracks, completely eliminating waste.
In-house Idea
As this point, to prevent stoppage of the machine, each of the yarn colours supplied to the machine would be pre-wound onto cones. The winding machines take a full cone of yarn from the warehouse and move in onto new cones, each one set to provide the maximum length of yarn that could possibly be required for that colour. Ryan’s idea involved identifying each cone as destined for the loom, and wind just the right amount onto it. Identification of the cone would be through the use of RFID (Radio Frequency Identification) tags, a contactless technology. Interface had begun work on this and had even taken out a patent on integration of an RFID chip into a cone.
Ryan had been an electrician, working on shifts to troubleshoot and repair issues that arose around the clock. He knew the shop floor equipment very well. He was passionate about the positive impact on the environment stemming from the organization he worked for. He had often discussed his plan to eliminate this waste. In fact, for a number of years, Interface’s tagline was ‘Mission Zero’ and Ryan, like so many of his colleagues, were wholeheartedly engaged in whatever way they could to drive towards this goal.
Ryan traveled regularly to the manufacturing headquarters in Holland, where the patent for the cone containing an RFID tag had been granted. He was aware of an attempt to build software into the PLC, the Industrial computer that controlled the winding machine. A workable solution had not yet been found.
A New Approach
One day, a new Engineer, Daire, arrived at the plant to begin work as an Engineering graduate. Picking up on each other’s enthusiasm, they went through the potential opportunities, obstacles and decided that together they could attempt a locally engineered solution. If the solution proved successful, they argued to senior management, it could become revolutionary for the Craigavon plant and would be just as applicable elsewhere.
Linkup with Meteor Software Limited
Having worked with the industrial PLCs that control machines within tyre factories, as well as the hardware used in RFID tags, Meteor Software just happened to be in the right place at the right time and we made known our expertise in this field.
We had several meetings to refine the suggested approach, before Ryan and Daire put together a proposal for capital expenditure, allowing them to explore further their idea.
The plan was to build upon a piece of work that David Dewhurst (Meteor Software Limited’s Software Engineer) had created a few years prior, using code that could communicate with the existing Mitsubishi PLC controlling the machine. A series of RFID readers would be mounted onto the machine – one for each post that wound yarn to length. A PC would be mounted at the end of the machine, running a program that Meteor Software would create, loading in settings for the lengths of yarn to be produced, communicating this with the PLC, writing that data to the RFID tag so that a scanner could be used later to indicate where the cone should be placed. Networking and electrical supply would have to be run in. An RFID scanner at the end of the conveyor, where the cones had been wound, would indicate to the operator which box to place the cone in, thereby reducing travel time for the operators loading the creel later on. Different boxes of pre-wound cones would be delivered to different parts of the creel.
Internal Capital Project Approved
Fortunately for Daire and Ryan, Interface has quite a few technically minded managers and their proposal was warmly received, even in a year where capital allocation was difficult to come by.
First Trials Never Go to Plan
The plan started up well. Early tests indicated that the software was able to read and write to the PLC just fine. Communication with the RFID tags was less reliable. The cones were spinning in the machine and the readers were picking up tags from adjacent posts. When trials were arranged, around ten percent of cones produced had no readable tag. A time lag was introduced to allow the cone to begin winding before attempting to read the tag, but it became apparent that this was not a good solution, as some very small runs required extremely short lengths of yarn on the cone.
Things were not going smoothly. At this point, Ryan and Daire were deciding what to do next. It seemed like their idea was falling apart. They were sure that they were onto something, but 90% good isn’t enough for 24/7 production.
Adapting to Overcome Obstacles
Sticking with the issues, and discussing each one with possible things to try, Daire adjusted the power going to the antennae, reducing it to avoid picking up adjacent cone values. Eventually, through reading the documentation on the readers, the advice was to have the four antennae controllers operate on differing frequencies, further reducing interference.
This left an issue with time taken to get the information onto the tag. It was not acceptable to slow down a machine for this purpose.
Through analysis again, the advice was to consider using the RFID tag as an identifying tag only, not to actually write data to it. Read operations were significantly quicker than write operations.
This suggestion didn’t sit well with everyone in Interface. Daire and Ryan had to work to convince some others that this was the way to go. It was a shift in understanding, and would require additional hardware for each plant where it would be rolled out. A handheld RFID reading device, operated in the creel workshop, would have to have Wifi access. A file storage system was required to hold the data that would up to now have been written to the tag.
Confident in the direction that they were moving towards, Daire and Ryan pressed on. The updated solution read the tag and stored the data in the file system within the PC.
The IT manager for the site wasn’t keen on this solution, as a hardware failure would render all wound cones unusable – as the handheld reader wouldn’t be able to associate the tag with a file in the PC telling it (and so the operator) where to load the cone.
Solution Agreed
A known solution to this was proposed and accepted. The Interface site installed a database and the code on the workshop floor was amended to now write the data not to the RFID tag or the local PC, but to the new database. This had other side benefits, in that the IT department could easily create simple reports on winding progress based on the database contents (total tags wound today etc. )
Industrial Levels of Quality Achieved
Finally, after many iterations, hard work and perseverance, the acceptable number of cones from a run reduced down to one or two out of a thousand. These were genuine RFID tag failures. An additional feature was requested and created, allowing the operator to re-run a cone that had been created but failed to be read at the end of the winder line.
Conclusion: Success for everyone
With several successful runs, the system now works very well for the plant. Documentation for the solution was put together to give the solution perennity. Ryan and Daire have both moved on to other things, and the roll-out for the solution is being planned within the Craigavon site, with great interest being shown from other sister plants.
Interested in Getting Started?
Contact us
Our team is on hand to help you get started with your project!