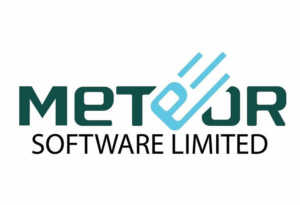
Client – Tyre Manufacturing
At our client’s tire manufacturing plant in North Carolina, we implemented a unique system to facilitate communication between the Allen-Bradley Control Logix PLC on each machine and our server. The system transmitted messages detailing sequence durations, ownership, stoppages, and more.
Ask for help with your industry
Innovation never stops
Assuring Machinery Performance
OEE Monitoring on a production machine
OEE
OEE, or overall equipment effectiveness is an internationally recognised method of assessing the performance of machinery.
Intro
Inside a production plant, such as that of our client – an International Tyre manufacturer in North Carolina, we worked to install a unique system to help the factory assess performance.
Linkup with Meteor Software Limited
Sam Rodgers works as the digitalisation lead for the plant in North Carolina and having previously worked in the United Kingdom (Ballymena and Dundee), he had seen and used similar systems built by the developers now working in Meteor Software Limited.
In this case, Sam worked with us to send messages from the Allen-Bradley Control Logix PLC which runs on each of the machines to Meteor Software’s server. The bespoke messaging indicates the durations taken to perform each of the sequences on the machine, with details relating to ownership, stoppages etc.
All the messages are received by our server, operating inside the secure factory network, and treated according to whether they indicate operator login, stoppages, unit completion etc. Using a database, we store relevant information and make summary calculations available to Industrial Engineering and Production Management.
We built a frontend website, customized so that different users log in using their organization’s LDAP credentials, granting access to different levels of reports, editing functions etc.
We’ve also recently evolved the product to include an automated tool, which allows an Industrial Engineer to select from products previously produced to refresh the theoretical time it should take to complete each of the sequences. We iterate over all the sequences for all the selected products and calculate the median, then update the recipe with the new theoretical. This allows the factory to review performance according to established norms, without having to go through the painful and time consuming practice of measuring manually with a stopwatch, especially useful following the introduction of a new SKU or a significant process change.
Interested in Getting Started?
Contact us
Our team is on hand to help you get started with your project!