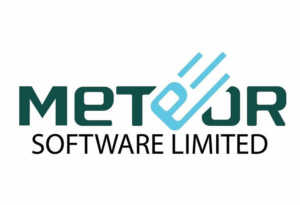
Client – Aircraft Tyre Manufacturing
The client, an international aircraft tire manufacturer in North Carolina, collaborated with us to enhance their production plant’s efficiency. We integrated a specialised system, linking up with Meteor Software Limited, to make their PLC-controlled machines smarter.
Ask for help with your industry
Innovation never stops
Making Machines Work Smarter
Recipe (Settings) handling system for machines
Intro
Inside a production plant, such as that of our client – an International Tyre manufacturer in North Carolina, we worked to install a unique system to help the factory assess performance.
Linkup with Meteor Software Limited
Our client manufactures aircraft tyres. The machines in their plant are controlled by PLCs, and so they engaged with us to build a solution for them to make those machines smarter.
Sam Rodgers works as the digitalisation lead for the plant in North Carolina and having previously worked in the United Kingdom (Ballymena and Dundee), he had seen and used similar systems built by the developers now working in Meteor Software Limited.
Each time a machine inside a factory builds a tyre, it uses a large number of customized settings. These settings change for different tyre types, and so we built a website frontend which allowed technicians to construct ‘recipes’. Various settings for speeds, durations, dimensions, thicknesses etc. are able to be stored, copied and shared as required – all within their internal secure network.
When required, a recipe is downloaded to the Allen-Bradley Control Logix PLC, ensuring that all the settings required are used to produce the same product each time a production run is required.
This takes away the need to take notes of different settings each run and manually enter them before restarting the same product – perhaps months or years later.
We also provided many reports, allowing quality professionals to review changes made to recipes over time, assess the differences between recipes used on similar machines etc.
The system has been such a success that as soon as it had completed live proving on one machine, it was requested by another workshop within the factory. As we go to press, a third workshop inside the plant has indicated that they too want to have a similar bespoke system for their machines.
Interested in Getting Started?
Contact us
Our team is on hand to help you get started with your project!